A Guide to Rebuilding Your Cold Former
- Jan 10, 2018
- 5 min read
Updated: Dec 5, 2022
Is your old cold former not answering the call to duty like it once did? After fighting TIR issues or unplanned machine downtime for months, you’ve concluded it’s time for some surgery. Here are some tips to help you minimize your expense and ensure that you get a good result.
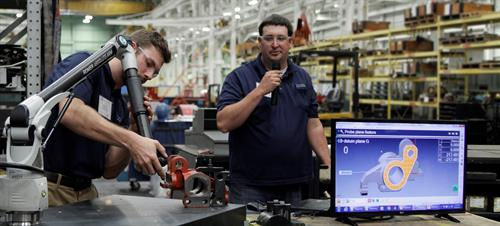
The first task is to get a clear diagnosis of the patient. Gather your operator and your maintenance staff together for a discussion with a knowledgeable rebuild technician. It’s important for your rebuilder to know what shortcomings you might be seeing in your finished parts, what observations your operator may have, and the maintenance and reliability history of the machine. Couple that with a hands-on machine evaluation and it will soon become clear whether your machine needs a complete rebuild, or if targeted repairs will suffice.
Once the scope of work is clear, there are several key points you should be sure to cover up front, and verify along the way to ensure you get the result you are targeting.
1. Get it right from the beginning
Inspection is the most important phase of the rebuild. While the discussion and evaluations described above are very helpful in planning the scope, the full condition of the machine cannot be known until it is torn down and inspected. If things are missed at this phase you will at best be looking at a delay during reassembly, and at worst an unplanned failure. For complete machine rebuilds, the machine should be completely disassembled down to the bed frame and components inspected against the original part prints.
Crack detection inspection should be done on all drive train components (die-penetrant and multi-wave ultrasonic) and hardness tests on running surfaces. In addition, there is now inspection technology available that can be applied to make a rebuilt machine “better than new.”
Back when your machine bed was machined, certain surfaces were likely measured only by the machine tool making the cuts. If that machine tool was slightly out of calibration, the cut and the measurement would have matched, but both would have been equally wrong. Today, CMM (Coordinate Measuring Machine) technology can help us ferret out any such issue quickly and simply, so that it can be addressed during the rebuild.
The portable CMM unit shown below can be set up directly on the bed frame of the machine, and used to scan bores and die pockets. This unit comes with software to allow the user to overlay the actual measurements onto a 3D image generated from the machine bed print. If you have access to the OEM prints, this tool makes it very easy to see what is needed to get the bed completely in compliance with the original design. The unit is portable, so it can be used even if the machine bed is not being moved for the rebuild.
2. Original prints
Rules of thumb about clearances in key mechanisms are often applied by rebuilders, as are substituted materials. The problem with this is that materials and clearances were chosen by the original designer based on specifics. Factors such as the precision required, the forces being transmitted and associated deflection, and the speeds involved were all accounted for in the design. These choices were then validated (and perhaps redefined) based on field experience. Applying “one size fits all” rules of thumb during rebuilding creates a shop-built prototype out of what was previously an engineered and field proven design.
Wherever possible, make sure your rebuilder has access to the original design drawings, and uses them during the rebuild. While conventional wisdom is that OEM rebuilders are more expensive, knowing is more efficient than guessing. Technicians working to print and using original fixtures not only should produce a better result, but can also usually get the job done more efficiently.
3. Relevant experience
The long service life of cold forming equipment as well as the huge range of applications has resulted in a very wide variety of machine models over the years. National Machinery alone has produced thousands of machines, including many different models often equipped with order specific specials.
It is important that the technicians performing repair and rebuild work have knowledge of the specific machine model being serviced. A broad experience in cold forming machine repair and rebuild is not enough to ensure a quality result – the experience needs to match the specific machine and job at hand.
4. Engineering guidance
To optimize the cost of the work, you’ll want to repair and re-use components in many cases. Doing so can be risky without the right technical guidance. Typical examples of repair questions which might arise during a rebuild are:
“The shaft diameter is worn .05” below original – can it be polished and re-used with an undersized bronze bearing?”
“What pre-heating and welding procedure should be used to weld repair this crack?”
Regardless of the experience level of technician involved, these questions need to be answered by a qualified engineer who is applying design guidelines. Rules of thumb can be costly. If deviations from the original design are made, it is important that these deviations are recorded for future use. At National Machinery, we do this automatically at the completion each rebuild as a service to customers. When a spare part is ordered even decades later, the deviation will be flagged at order entry, and the part shipped will be customized to match the machine. 5. Design Upgrades The last 25 years have witnessed a huge advance in the speeds and the precision with which parts can be cold formed. While it may not be realistic for your 30 year old machine to be upgraded to the same performance level as today’s designs, it is very likely that an upgrade can be applied that will make your machine more flexible, more safe, or more reliable than it is today. Make sure to discuss with your rebuilder up front what upgrades should be considered for your machine. If you own a National FORMAX machine, the modular design concept of FORMAX lends itself to easy “bolt on” upgrading. A very wide range of upgrades have been captured and packaged for retrofit; kick-out, transfer, and controls upgrades are most commonly implemented. Transfer upgrades are a very common upgrade for older machine models. Adding a Universal transfer can enable forming of a broader range of parts on the machine, which can allow you to add new business, or free up capacity on other machines. 6. Validation Before recommissioning, each rebuild should be tested and validated. For partial rebuilds or repairs this can be tricky, but often still possible. For example, if the feed and cutoff areas were overhauled, it is possible to validate results by taking cutoff blank samples at varying speeds and feed lengths – and weighing them to analyze any variation. For complete machine rebuilds, send your production-proven tools to the rebuilder to produce parts, and check the TIR of the parts to ensure consistency of the machine. At National Machinery, we’ve also invested in thermographic scanning equipment which is used during the machine “run in” to easily identify any lubrication or clearance issues. These images are then stored and can be used as a benchmark for any field troubleshooting down the road. Ask your rebuilder to share with you the results of the validation. Assuming you are satisfied, your soldier is ready for redeployment. Keeping these points in mind should help you to get the most from your next rebuild project, and allow you to reap the benefits for many years to follow. National Machinery is a capable and experienced partner to help you through all phases of your rebuild project. Please contact us via www.nationalmachinery.com or contact your local Sales Manager for more information. By: Mike Burkes, Senior Vice President: Service
Comments